Best Practices & Policies During COVID-19
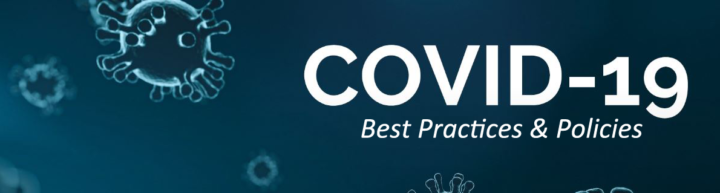
Due to the novel Coronavirus (COVID-19) outbreak, Tool Gauge is taking every precaution to keep our employees, their families, customers, and suppliers safe during this epidemic.
Based on the stay-at-home order from Governor Inslee on March 23, 2020, and the temporary shutdown of Boeing Puget Sound, Tool Gauge temporarily shut down from March 26 through April 16th.
As we plan to bring back partial crews to support non-Boeing Puget Sound shipments, Tool Gauge leadership and management teams have placed COVID-19 best practices to keep everyone safe and healthy while in the office and on factory floors. Best practices include prevention, protection and containment strategies:
Prevention
- • Informed employees of COVID-19 symptoms to watch for through CDC approved fliers, signage, and updates posted on internal applications.
- • Signage with enhanced PPE requirements has been posted throughout metals and plastics facilities near time clocks.
- • Nitrile gloves, safety glasses, face masks, and hearing protection have been provided to all employees working.
- • PPE are placed in optimal areas near doors and time clocks for distribution with clear explanations of proper usage.
- • Common areas such as lunchrooms, bathrooms, conference rooms, and all doors will be cleaned 4 times daily. Cleaning logs have been implemented and placed in each area, requiring a date, time and employee number of when it was cleaned.
- • All doors are to remain open to reduce exposure.
- • Signs are posted throughout both facilities to encourage people to wash their hands frequently, using soap, and washing for a minimum of 20 seconds.
Protection
- • Social distancing is in place, with a 6 ft separation policy in place. We’ve taped X’s and lines throughout both facilities indicating where people should stop when approaching work cells.
- • Break times have been staggered to allow a minimum of 6 ft separation at lunch tables.
- • Cleaning stations have been placed throughout offices and on the factory floors. Employees have quick access to cleaning equipment such as disinfectant wipes, paper towels, Lysol spray, etc.
- • Implementation of self-check screening tools.
- • Restricted all international business travel and any external meetings and personnel.
- • Staff who can work remotely have been encouraged to do so.
- • Communicate with all staff via email and internal applications on COVID-19 updates and temporary shutdown dates
- • Producing DtM Face Shields for Washington State, click here for DtM Face Shield assembly steps and instructions for use
Containment
- • Mandated quarantine for employees testing positive for COVID-19.
- • Identify and contact employees who may have been in contact with employee(s) displaying symptoms and mandate quarantine.
- • Close contaminated work area or facility.
- • Start disinfection procedures of contaminated areas.
Best practices have been distributed through multiple forms of communications via posted flyers in both metals and plastics divisions, internal applications and emails, and social media. We will continue to update our employees, customers, and suppliers of our best practices, temporary shutdown updates, and COVID-19 news in the Puget Sound region.
For more information on preventing the spread of COVID-19 and other respiratory illnesses, visit the CDC or your state’s Department of Health website.
If you are interested in purchasing Face Shields from Tool Gauge, please click here for more information or contact us at sales@toolgauge.net.