Facility Expansion Update – Summer 2019 Part 2
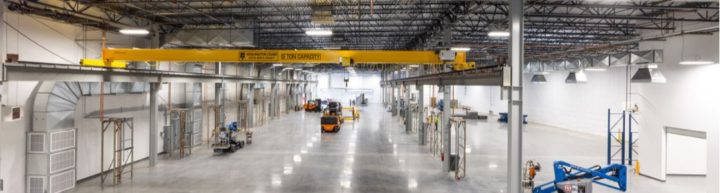
If you’ve been following along our social media pages and watching our Workzone Cam, you might have noticed some significant progress to the Tool Gauge facility expansion project. We’re excited to say, we have officially occupied Phase 1 of construction!
During July, Washington Patriot Construction wrapped up a few projects to get ready for our scheduled August move-in date along with receiving a very heavy delivery. Washington Crane and Hoist delivered and installed our shiny, new 5- and 15- ton overhead cranes which will assist employees in moving molds from tool storage to designated machines throughout the new facility.
August was one of the busier months as we finalized exterior and interior projects of our new facility in preparation for occupancy starting on the 23rd. Exterior paint was completed earlier in the month as Washington Patriot Construction worked to install gutters, downspouts and bathroom sinks and partitions. Before the floors were sealed, the interior walls got a fresh, white coat of paint and two shiny blue air compressors were placed in the mechanical room.
As soon as the major items were built in, floors were sealed to get ready for final touches including air barrier testing. Tacoma based company, Nexus BEC, performed the air barrier test which measures how much air leaks through the building’s envelope. This type of test is required for all new heated buildings to receive a certificate of occupancy – we passed with flying colors!
August 23rd marked the first day for our Plastics Secondary Operations and Shipping departments to move. Both areas worked throughout the weekend to move product, tools, equipment and work stations, enabling production and assembly to continue as scheduled the following Monday.
Both teams will continue to reorganize their departments to prepare for CNC machines and plastic injection molders to be moved from our current production facility in mid-September. Industrial racks have been built in two areas of the new facility, finished goods and mold maintenance, to better assist teams in their organizational processes. Management has incorporated new LEAN initiatives including designated hardware racks, which will allow for easier accessibility and movability of finished parts and molds through the facility.
As Phase 1 wraps up, we look forward to moving our CNC machines, tool room, and plastic injection molders starting on Sept 19th – Oct. 2nd. All machines will have to be disconnected, moved, then re-connected and calibrated over this specific time period. Once completed, Phase 2 demolition started on Monday, Oct. 7th.
Phase 2 of the expansion is estimated to be completed late 2019. It will include the demolition of our current plastics facility to build our paint department, QA lab, training and lunchroom area, employee lockers and restrooms, offices and facility entrance/lobby. Other important expansion details include:
- •An additional 80,000 sq. ft. in our plastics division
- •Expansion of our plastics press size range
- •Broadened secondary operations, improving flow and ergonomic assembly
- •Installation of a state-of-the-art vertical paint system
- •New research and development center
- •Implementation of multiple collaborative robots (cobots)
- •An additional 2,000 sq. ft. for CNC machines and equipment within our metals division
As the expansion project concludes, we expect to create over 100 new jobs spanning over the next five years within the Tacoma-Pierce County region. The Work Start Grant from Governor Inslee’s Strategic Reserve Fund will assist in training of new employees and advance the skills of 50 incumbent employees. Employment opportunities are listed on our career page and are continually updated with positions ranging from full-time opportunities in machining, molding, assembly and engineering areas.
To receive more information on our expansion process and on-goings at Tool Gauge, sign up for our quarterly newsletter, here.