Tool Gauge and the relentless pursuit of technology
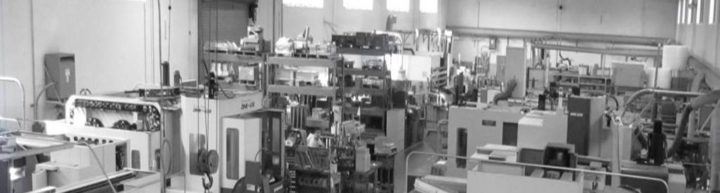
While the expansion of our Tacoma manufacturing facility moves forward, we continue to invest in our leading-edge manufacturing capabilities. We are in the middle of a program to replace all of our hydraulic presses with new, all-electric machines that provide better process control, are much quieter, more energy efficient, and easier for our staff to operate. This allows us to reduce scrap, improve flow times, and provide better overall customer support. We have recently added the following innovative equipment to our factory floor:
FARO Edge Scan Arm HD
The FaroArm Edge is a portable coordinate measuring machine (CMM) that allows us to easily verify product quality by performing 3D inspections, tool certifications, CAD comparison, dimensional analysis, reverse engineering, and more. This is the most useful tool in our arsenal as it allows us to create rapid multi-3D data comparisons. Tool Gauge has developed a highly accurate process that improves the efficiency and accuracy of the plastic part qualification process. This machine also provides us with the benefit to establish the most accurate and repeatable injection molding manufacturing methods possible. FaroArm Edge inspection processes are currently utilized on many of the BAC 5321, Class 2 programs that are now in development at Tool Gauge.
Doosan Puma TT1800 SY with Bar Feed (CNC Lathe)
The Puma 1800Series is a 65mm (2.6 inch) bar capacity, high-productivity horizontal turning center that is equipped with twin-opposed spindles and upper / lower turrets with live tool capability. The left and right spindles can process work pieces independently to achieve excellent productivity.
Our Puma system is fitted with a LNS Quick Six S2 automatic bar feeder that can load six-foot-long bars with diameter ranges from 3/8” to 3-1/8”. It allows us to produce cost-effective, short lead time-turned components.
IL-885 Automated Media Blasting System
Our new media blast system provides rapid precision surface treatment for metals and plastics, including BAC 5748 Type 2, Class 1 surface preparation. This is a six-head conveyor system with variable speed controls and adjustable parts guides that provide the versatility to deburr, clean, profile, and finish parts of many different shapes and sizes ranging from tubular to flat. If two sides of a work piece require blasting, the piece can be reloaded for a second pass. Questions about our advanced plastic or metal assembly manufacturing capabilities? Learn more about our injection molding equipment or email Sales & Marketing Manager Jim Lee.